U.S. Factories Face Labor Shortages Amid Nearshoring Boom:
The U.S. manufacturing sector is experiencing a significant labor shortage as nearshoring trends continue to drive production closer to home. With companies moving their supply chains from overseas to North America to reduce logistical risks and enhance efficiency, the demand for skilled workers has surged. However, factories across the nation are struggling to find enough talent to fill critical roles.
Why Nearshoring Is Booming in the U.S.
Nearshoring—relocating production from distant offshore locations to closer markets—has gained momentum due to several factors:
- Supply Chain Disruptions: Global events, such as the COVID-19 pandemic and geopolitical tensions, exposed vulnerabilities in long supply chains, prompting companies to seek localized solutions.
- Rising Costs Abroad: Increasing wages and shipping costs in traditional manufacturing hubs like China and Southeast Asia have made domestic production more attractive.
- Government Incentives: Federal and state-level policies, such as tax credits and infrastructure investments, are encouraging businesses to invest in U.S. manufacturing.
Despite these advantages, the biggest challenge remains the availability of skilled labor. The National Association of Manufacturers (NAM) estimates that over 3.8 million manufacturing jobs will need to be filled within the next decade, and failure to address this gap could stifle the growth of nearshoring efforts.
The Labor Shortage Challenge
U.S. factories are facing hiring difficulties due to several key factors:
- Aging Workforce: Many skilled workers from the Baby Boomer generation are retiring, leaving a significant skills gap in the industry.
- Lack of Interest from Younger Generations: Manufacturing jobs are often perceived as outdated or low-paying, discouraging younger talent from pursuing careers in the sector.
- Skills Mismatch: With technological advancements, factories now require workers with specialized skills in automation, robotics, and advanced machinery—skills that are not widely available in the current labor market.
Efforts to Close the Skills Gap
Manufacturers are taking various steps to attract and train new talent, including:
- Apprenticeship Programs: Companies like Blum USA have partnered with educational institutions to offer on-the-job training that combines classroom learning with practical factory work.
- Technology Integration: Employers are investing in automation and artificial intelligence to reduce reliance on manual labor while enhancing productivity.
- Marketing Manufacturing Careers: Organizations are working to rebrand manufacturing as a high-tech, high-paying career path to appeal to younger generations.
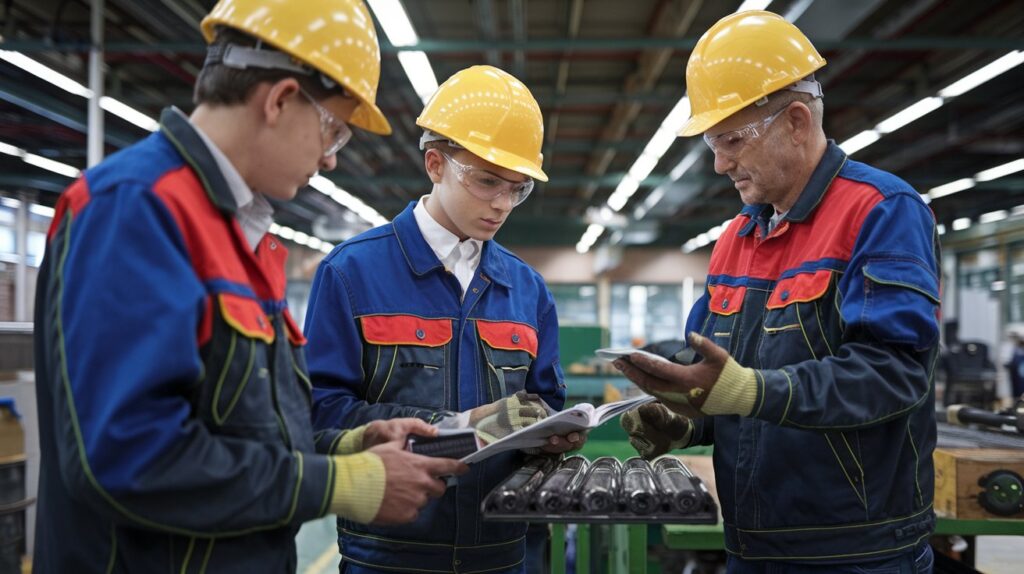
Industries Most Affected by Labor Shortages
Certain sectors within U.S. manufacturing are facing more acute labor shortages than others, including:
- Automotive Manufacturing: As the demand for electric vehicles (EVs) surges, automakers are investing heavily in domestic production but struggling to find skilled technicians.
- Semiconductor Industry: The U.S. government’s push to increase chip production domestically is creating thousands of new jobs, but training skilled labor for these positions takes time.
- Construction Materials: Nearshoring has boosted demand for construction-related materials, yet labor shortages have slowed production capacity.
The Road Ahead: What’s Next for U.S. Manufacturing?
While nearshoring offers a promising future for American manufacturing, addressing the labor crisis will require a multi-faceted approach. Employers, policymakers, and educational institutions must collaborate to reshape perceptions of factory jobs and invest in upskilling initiatives.
If successful, the nearshoring boom could lead to a resilient U.S. manufacturing sector, reducing reliance on overseas suppliers and ensuring long-term economic growth. [USnewsSphere.com]